Podkłady kolejowe – fundamenty transportu szynowego
Podkłady kolejowe to elementy infrastruktury, które mimo że często pozostają niezauważone przez podróżnych, pełnią kluczową rolę w funkcjonowaniu całego systemu kolejowego. Odpowiadają za prawidłowy rozkład sił podczas przejazdu pociągów i utrzymanie stabilności torów [3]. Bez odpowiednio trwałych podkładów bezpieczeństwo i komfort podróży byłyby niemożliwe do osiągnięcia.
Kiedy pociąg przejeżdża po torach, generuje ogromne siły, które muszą zostać rozłożone i zamortyzowane. To właśnie zadanie podkładów kolejowych – przenoszą one obciążenia z szyn na podsypkę, zapewniając stabilność całej konstrukcji [3]. Dlatego tak istotne jest, aby materiały używane do ich produkcji charakteryzowały się odpowiednią wytrzymałością i odpornością na różnorodne czynniki.
Trwałość podkładów kolejowych zależy od wielu czynników – materiału, z którego zostały wykonane, procesów impregnacji oraz warunków użytkowania [1][2]. Warto zgłębić tajemnice tej trwałości, aby zrozumieć, jak inżynierowie kolejowi przez dziesięciolecia radzili sobie z wyzwaniami, jakie stawia przed nimi natura i eksploatacja.
Historia impregnacji podkładów drewnianych
Drewno było pierwszym materiałem powszechnie stosowanym do produkcji podkładów kolejowych. Jego naturalne właściwości – dostępność, elastyczność i łatwość obróbki – sprawiły, że przez długi czas dominowało w infrastrukturze kolejowej. Jednakże drewno w swoim naturalnym stanie ma jedną poważną wadę – jest podatne na degradację biologiczną i atmosferyczną [1].
Aby przeciwdziałać tym niekorzystnym procesom, już w XIX wieku zaczęto stosować różne metody impregnacji. Początkowo używano smoły drzewnej i oleju kreozotowego, które skutecznie chroniły drewno przed grzybami i owadami [3]. Kreozot, uzyskiwany podczas destylacji smoły węglowej, przez dziesięciolecia był najpopularniejszym środkiem impregnacyjnym, jednak ze względu na jego toksyczność i kancerogenność, jego zastosowanie zostało znacznie ograniczone w ostatnich latach [1].
Proces impregnacji podkładów drewnianych ewoluował na przestrzeni lat. Pierwotnie stosowano metodę kąpieli, polegającą na zanurzaniu podkładów w gorącym roztworze impregnatu [3]. Z czasem rozwinięto bardziej zaawansowane techniki, takie jak metoda ciśnieniowa Bethella, która pozwalała na głębszą penetrację środka konserwującego do struktury drewna [1]. Proces ten polegał na umieszczeniu podkładów w szczelnych cylindrach, wytworzeniu próżni w celu usunięcia powietrza z porów drewna, a następnie wprowadzeniu impregnatu pod ciśnieniem.
Rodzaje impregnacji i ich wpływ na trwałość
Wybór odpowiedniego środka impregnacyjnego i metody jego aplikacji ma kluczowy wpływ na trwałość podkładów kolejowych. W historii kolejnictwa stosowano różne substancje, każda z nich charakteryzowała się odmiennymi właściwościami i skutecznością [1][3].
Oprócz wspomnianego kreozotu, popularnymi impregnatami były sole miedzi, chromu i arsenu (CCA), które zapewniały dobrą ochronę przed czynnikami biologicznymi [1]. Z czasem, ze względu na szkodliwość arsenu dla środowiska, zastąpiono je nowocześniejszymi kompozycjami, takimi jak CCB (sole miedzi, chromu i boru) czy CCFZ (sole miedzi, chromu, fluoru i cynku) [3].
Nowoczesne impregnaty to zazwyczaj wodne roztwory soli, które są znacznie bezpieczniejsze dla środowiska naturalnego niż ich historyczne odpowiedniki [1]. Jednak ich skuteczność w przedłużaniu żywotności podkładów bywa różna, dlatego wciąż trwają prace nad opracowaniem optymalnych środków ochrony drewna dla zastosowań kolejowych.
Wpływ rodzaju drewna na skuteczność impregnacji jest również istotnym czynnikiem. Gatunki o zwartej strukturze, takie jak dąb czy buk, są trudniejsze do nasycenia impregnatem, ale naturalna odporność tych gatunków często rekompensuje ten problem [1][3]. Z kolei sosna, która jest łatwa do nasycenia, ale mniej odporna naturalnie, po odpowiedniej impregnacji może osiągnąć bardzo dobry stosunek jakości do ceny.
Czynniki wpływające na żywotność podkładów
Trwałość podkładów kolejowych nie zależy wyłącznie od zastosowanych środków impregnacyjnych, ale od kompleksu czynników, które oddziałują na nie podczas eksploatacji [1][2]. Zrozumienie tych zależności pozwala na optymalizację procesów produkcyjnych i utrzymaniowych.
Jednym z najważniejszych czynników jest rodzaj materiału użytego do produkcji podkładów. Różne gatunki drewna charakteryzują się odmienną naturalną odpornością na czynniki biologiczne i atmosferyczne [1][3]. Na przykład podkłady z drewna azobe, które jest niezwykle twarde i odporne na gnicie, mogą służyć nawet do 50 lat [1]. Z kolei podkłady sosnowe, bez odpowiedniej impregnacji, ulegają degradacji już po kilku latach.
Warunki klimatyczne i atmosferyczne mają również ogromny wpływ na trwałość podkładów. Wilgotność, temperatura, nasłonecznienie czy kontakt z gruntem – wszystkie te czynniki przyspieszają procesy degradacji materiału [1][2]. Dlatego też podkłady eksploatowane w różnych strefach klimatycznych mogą wykazywać odmienną żywotność, nawet jeśli zostały wyprodukowane w ten sam sposób i z tego samego materiału.
Obciążenia mechaniczne, jakim poddawane są podkłady podczas eksploatacji, również wpływają na ich trwałość [2]. Linie o dużym natężeniu ruchu i wysokich prędkościach pociągów generują większe siły działające na nawierzchnię kolejową, co przyspiesza zużycie podkładów. Z tego powodu na liniach magistralnych często stosuje się podkłady o podwyższonych parametrach wytrzymałościowych lub częściej wymienia się zużyte elementy.
Podkłady betonowe – alternatywa dla drewna
W odpowiedzi na wyzwania związane z trwałością podkładów drewnianych, w XX wieku zaczęto wprowadzać podkłady betonowe, które obecnie stanowią dominujący rodzaj podkładów na wielu liniach kolejowych [2][3]. Ich główną zaletą jest długa żywotność, sięgająca od 35 do 50 lat, w zależności od natężenia ruchu [2].
Podkłady betonowe, w przeciwieństwie do drewnianych, nie wymagają impregnacji, co eliminuje problemy związane z toksycznością środków konserwujących [2]. Składają się z betonu wysokiej jakości oraz zbrojenia, które zapewnia im odpowiednią wytrzymałość na rozciąganie [2]. Dzięki temu są odporne na większość czynników, które degradują podkłady drewniane.
Jednakże, mimo długiej żywotności, podkłady betonowe również podlegają procesom starzenia. Badania wykazały, że ich mrozoodporność maleje o 25-30% po 10 latach eksploatacji [2]. Ponadto, ze względu na sztywność betonu, podkłady te generują większy hałas podczas przejazdu pociągów i słabiej tłumią drgania niż ich drewniane odpowiedniki.
Innym problemem związanym z podkładami betonowymi jest ich masa – są one znacznie cięższe od drewnianych, co utrudnia transport i układanie [2]. Dodatkowo, w przypadku wykolejenia, uszkodzenia podkładów betonowych są zazwyczaj bardziej kosztowne w naprawie niż uszkodzenia podkładów drewnianych.
Nowoczesne rozwiązania i przyszłość podkładów kolejowych
Współczesne kolejnictwo stoi przed wyzwaniem znalezienia materiałów, które łączyłyby zalety podkładów drewnianych i betonowych, jednocześnie eliminując ich wady. Odpowiedzią na te potrzeby są kompozytowe podkłady kolejowe, które zyskują coraz większe zainteresowanie w branży [1][2][3].
Materiały kompozytowe, zazwyczaj składające się z polimerów wzmacnianych włóknami, oferują doskonałą odporność na czynniki biologiczne i atmosferyczne, nie wymagając przy tym impregnacji [1]. Charakteryzują się również długą żywotnością, porównywalną z podkładami betonowymi, przy jednoczesnym zachowaniu elastyczności zbliżonej do drewna [3].
Oprócz kompozytów, prowadzone są również badania nad innowacyjnymi metodami impregnacji drewna, które byłyby skuteczne, a zarazem przyjazne dla środowiska [1][3]. Eksperymentuje się z biodegradowalnymi środkami ochrony drewna, które nie zawierają toksycznych związków, a jednocześnie zapewniają odpowiednią ochronę przed czynnikami biologicznymi.
Przyszłość podkładów kolejowych prawdopodobnie będzie należeć do materiałów, które zapewnią optymalny balans między trwałością, kosztami, właściwościami użytkowymi i wpływem na środowisko [1][2][3]. Biorąc pod uwagę postępujące zmiany klimatyczne i rosnącą świadomość ekologiczną, można oczekiwać, że branża kolejowa będzie dążyć do rozwiązań coraz bardziej zrównoważonych.
Podsumowanie – tajemnice długowieczności podkładów kolejowych
Tajemnica trwałości podkładów kolejowych tkwi w kompleksowym podejściu do ich projektowania, produkcji i utrzymania. W przypadku podkładów drewnianych kluczową rolę odgrywa odpowiednia impregnacja, która przez dziesięciolecia ewoluowała od toksycznych substancji smolistych do nowoczesnych, bardziej ekologicznych rozwiązań [1][3].
Żywotność podkładów kolejowych to wypadkowa wielu czynników – od wyboru materiału, przez procesy technologiczne, po warunki eksploatacji i utrzymanie nawierzchni [1][2]. Podkłady drewniane, przy odpowiedniej impregnacji, mogą służyć od 12 do 50 lat, w zależności od gatunku drewna [1]. Z kolei podkłady betonowe, mimo że nie wymagają impregnacji, charakteryzują się żywotnością od 35 do 50 lat [2].
Przyszłość rysuje się w kierunku materiałów kompozytowych i rozwiązań hybrydowych, które będą łączyć zalety tradycyjnych materiałów, jednocześnie eliminując ich wady [1][2][3]. Niezależnie jednak od stosowanych materiałów i technologii, podkłady kolejowe pozostaną fundamentalnym elementem infrastruktury kolejowej, od którego zależy bezpieczeństwo i komfort podróży.
Źródła:
[1] https://ikolej.pl/wp-content/uploads/2024/10/Materialy_kompozytowe_na_podklady_kolejowe.pdf
[2] https://www.rynek-kolejowy.pl/wiadomosci/jakie-czynniki-wplywaja-na-trwalosc-podkladow-kolejowych-74355.html
[3] https://rockmatic.pl/podklady-kolejowe-drewniane
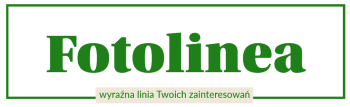
Fotolinea.pl to nowoczesny portal informacyjny działający pod hasłem „Wyraźna linia Twoich zainteresowań”. Dostarczamy rzetelne i inspirujące treści z różnych dziedzin życia, łącząc profesjonalizm z praktyczną wiedzą. Nasz zespół ekspertów każdego dnia pracuje nad tym, by zapewnić czytelnikom wartościowe materiały wspierające ich rozwój osobisty i zawodowy.